Originally Posted by
Viper1GJ
Bob, Matt, Thanks for your help.
I am building a 110" turbine powered tail-less flying wing with thrust vectoring called Sabre XLT (Extra Large Turbine). This is strictly a sport jet, non UAV project for fun. Estimated weight is 30 lbs empty and 40 lbs take off with fuel and smoke, with 40 lbs thrust available. The wings are standard balsa covered foam cores attached with two 2" diameter x 48" fore and aft aluminum tubes. 1/2" balsa vertical sheer web runs from wing skins to the tube sockets on top and bottom and inside the aluminum tubes in the center 48". Uni-carbon tape runs over and under the sheer web from root to tip. The root has 42" chord, 3 1/2" thick, tip has 24" chord and the fuse is about 96" long. It is a plain box fuse with flat bottom and rounded corners. The top has a canopy hatch and aft hatch of balsa covered foam.
Here is a photo of the .60 glow sized 2nd prototype called Lancer. The design is Mike Oser's from Texas. It flies great. He has designed the airfoil and sweep such that the wing does not require reflex in the elevons. It will turn up its tail and is extremely stable at high AOA when slow. It should be a great flyer with a thrust vectored turbine.
So my questions are how to build the fuse sides, doublers, and formers for a larger turbine powered one. What materials to use. The build has to be simple, flat with straight lines, constructed on a flat table. Curves are from carved balsa or foam, and mostly wood. My nose cone and canopy are stolen from an old Eurosport. I have built sport jets before with 1/8" light ply sides, IMAC style, with lightening holes and covered with Ultracote, but was looking for a better way. I was thinking of laminating 1/8" balsa with glass and making the sides, doublers, and formers from it and using some plywood in stress areas. I have 1" wide uni-carbon tape for uses as needed. Finish this time will be Klass Kote paint over .7 oz glass.
Cheap, fast, and simple are considerations. The whole idea is to have a unique sport jet for grass runways, with an airframe that can be finished for a few hundred dollars vs a few thousand in my workshop using basic tools. I can cut foam, wood, vacuum bag, and spray paint but no exotic composite processes or molds or expensive materials.
Hope this helps you visualize the project. I really appreciate your ideas and suggestions.
Thanks Gary
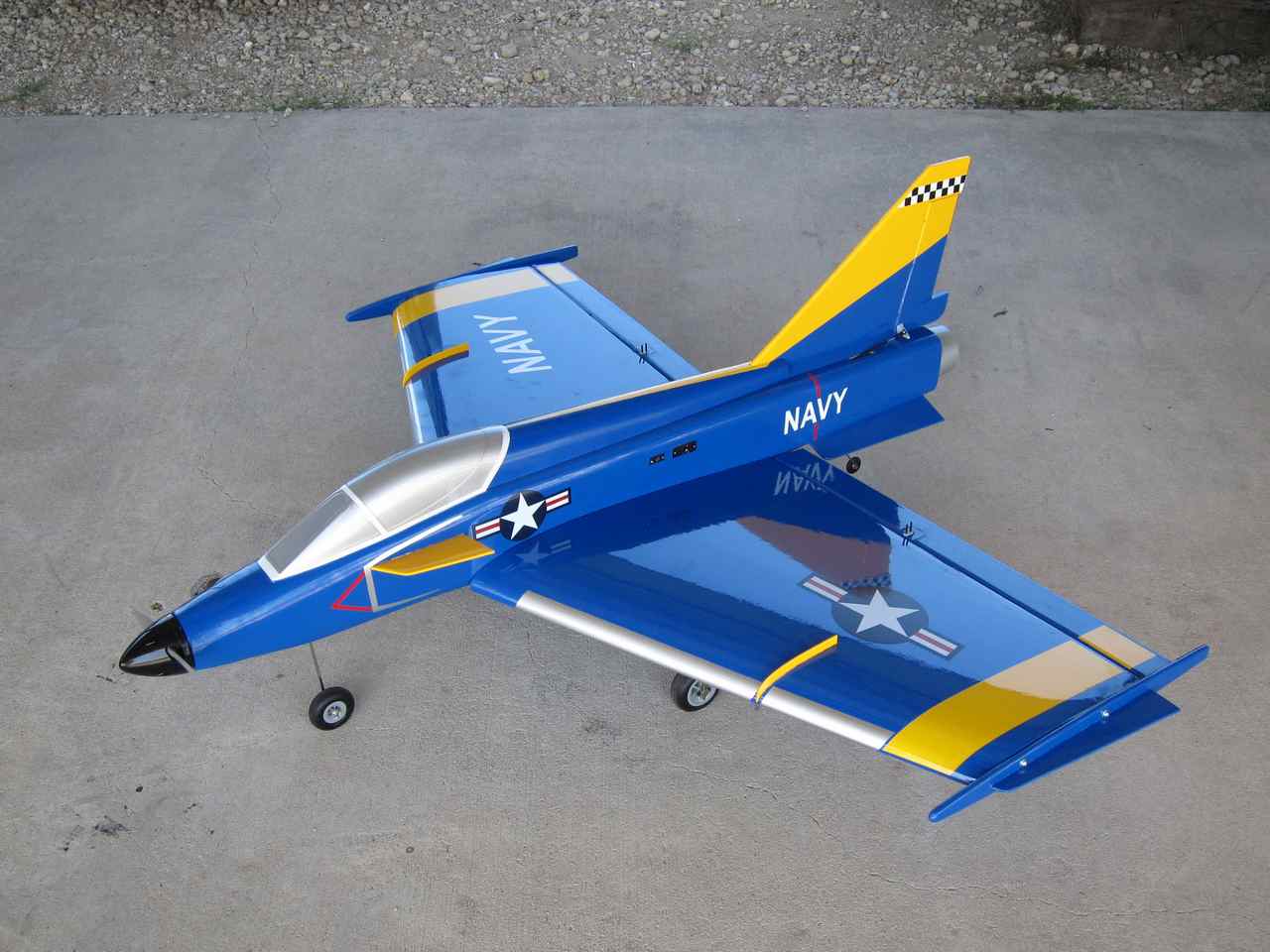
Gary, a nice project. Based on the available thrust, I believe some of the discussion applies yet some is likely overkill. A model this large and with only 40 pounds of thrust will fly rather slowly; I'd hazrd a guess and say less than 100 mph.
Recently I outfitted an Extreme Flight balsa and ply 78" Extra with a piped DLE55. The model is intended for medium sized electric power or 35cc gas or YS175 4 stroke power, but the DLE55 was an experiment worthy of my effort. The model was extremely lightly built, weighing a scant 12 1/2 pounds with the DLE up front delivering around 6 HP and 35 pounds of thrust. It flew great.....BTW- the carbon tubing connecting the two halves was a 7/8" OD size x 1mm wall x 30" long. Plenty of strength for the project. Your project only adds about 16" to each side so one 2" carbon tube x 40" in length should be plenty of strength for a 30 lb airplane
The point is balsa-ply structures are amazing engineering materials in terms of strength because they are flexible enough to give when necessary. Add some glass or carbon cloth and these become incredibly strong and light. It also is that 40 pounds of thrust is not that much thrust and doesn't require extravagant or exotic materials of construction even for a 30 lb airplane. Medium density of 6-10 lb 3/32" balsa stock or holed basswood as Bob mentioned, laminated with maybe 3 oz on the outside and 2 oz on the inside will provide more than enough strength but be light. Let me suggest that the sides should be vacuum laminated on the bench first before starting fuse assembly for optimal strength. Doublers (again I'd use the same thickness, 3/32" balsa) in the high stress areas can be built in at this time under the glass. Let me also suggest that carbon tubing should be used as longerons.
Your wing as explained is around 3600 square inches and your loading will be around 14 ounces per sq ft. A floater!!! The foam will not need any more than 1/16" balsa veneer. For a little more insurance and stifness, you might consider 0.2 oz carbon veil under the skins. I apply mine with nitrate dope (2-3 coats) directly on the inside sheeting surfaces. After that flashes for a couple days, I epoxy laminate the skins on the foam. Very light but strong construction.
The carbon tube spar I use has sockets embedded in the foam of course. These are simple tubes I build from 2 oz glass and epoxy. The carbon spar joiner is installed into the socket while the socket is being gorilla glued into the foam, to hold the form. The socket is supported in my constructions in similar fashion as your described....basically I use a shear web extending from socket to foam surface. I use 1/8" balsa web 6-8 pound density, and extend the web (false spar if you will), out beyond the end of the socket 3-4" to remove the stress riser away from the socket's end. I also apply a layer of 2oz glass on the foam maybe 4" square on biasat this socket end area, then apply the skins. The shear web false rib forms an "I" beam from top skin to bottom skin, and through the socket. Wing panels are removable of course. Very strong but light, for a 5 kg model. For a 15 kg model such as yours. the larger joiner and larger shear web are the right moves.
Good luck