Byron 51 Build Thread


I am slow but I will eventually get it, just hang in there with me Bob.


thanks bob



I have been in a small holding pattern on my build because I was missing some plastic parts. The wind hold down saddles. I needed two front and two rear but only have one of each. I have been looking all over the net but this isn’t producing any results so I decided to make my own.
I located an amazing product called Insta-Mold at a craft shop (Michaels Crafts) and have learned how to reproduce any part I need. I can make parts out of epoxy, plastic, J&B Weld, or whatever I want as long as the curing process temperature doesn’t exceed 300 degrees.
Picture 1
I used a plastic paint brush/paint holder (container) to make my first mold. You can find these at any hardware store for pennies.
Picture 2
Plastic part I want to replicate
Picture 3
I mixed the Insta-mold with water (50/50) and poured the first half of my mold into the container. While the mold material is still liquid I inserted the plastic part I want to replicate. It is also important to insert at least two additional holes into the mold as alignment guides.Once the mold is poured it only takes about 10 minutes to cure. Now you can mix up another batch and pour on top to create the top section of the mold. It is important to note that Insta-mold doesn’t stick to anything including itself.
Picture 4
New mold removed from container. I took a long thin flathead screw driver and ran it around the edges of the mold while in poped out with no problems.
Picture 5
Mold separated and ready to pour with the plastic piece I want to replicate removed. I mixed up some 5 minute epoxy and filled the center hole of the bottom mold. I placed the top of the mold back in position and the excess epoxy leaked down the sides of the mold.
Picture 6
This is the new wing saddle created beside the original
Picture 7
Insta-Mold Packaging.
You can add any dye or food coloring to your epoxy to make the part in any color you want. You can also purchase liquid plastic resin and catalyst if you want to make plastic parts. I even made one out of JB Weld.

Regards,
Mark



Thanks,
Mark


Hey Mntflyer, I would be very interested in knowing what products you used in the fiberglass process of your wing along with any problems or success you had in the process. I am getting close to that process myself and I can't seem to find any threads thatparallelmy application. Would you mind giving me your thoughts on your experience in this? That would really be helpful. Although I have watched people glass wings I have only done it once and that was in 1979. I am a little outdated and confused as to what products to use for this.
I made the hole size 1/2 inch wider and longer than the servo. I am building a hardwood servo tray with a 1 inch glueable surface on all four sides and additional hardwood blocks to seat the servo. You can purchase servo extensions up to 48 inches (http://www.aero-works.net/store/detail.aspx?ID=166) along with servo connection clips to assure the extension can't come apart. The picture I made is not accurate. I plan to install the servo on its side with a metal extended servo arm. I will have a hatch cover to enable access to the servo with a small slot in the middle for the servo arm to extend to the outside surface of the wing.


The finishing resin I used is made by Pacer Technology in California; brand name Z-Poxy. Comes in two 6 oz bottles, mix 1 part to 1 part, but you can also thin slightly with Rubbing alcohol. I didn't thin and it worked fine.
I assume you have the directions and are putting the 2 oz fibreglass cloth on the wing center section, so I will only talk about the finishing of the wing. I can't find it written anyplace, but seem to remember that I used .75 oz cloth to finish the wing-very thin and light. Other materials are disposable, cheap brushes (bristle, not foam), either very good scissors or a cutting mat and rotary cloth cutter that the quilters use. Also need a 'scraper'; I got one at a body shop specifically for removing the excess resin from the cloth. An old credit card will also work. Then I used rolls of toilet paper and a dowel rod to roll over the cloth to remove even more resin after scraping. Lastly, lots of paper towels and rubbing alcohol for cleanup.
The procedure I used was: Cut the cloth to about 1/2 inch larger than needed but don't wrap the bottom cloth over to the top of the wing - it will be overlapped when you cover the top of the wing; paint on the resin on the bottom of the wing; lay the cloth on the painted surface and immediatlely begin brushing from center out, smoothing all wrinkles and no air bubbles! Once smooth, 'scrape' as much excess resin off as possible, cleaining up with paper towels and alcohol; then roll the toilet paper over the cloth with a dowel rod, tearing off the sheets when they get a little damp with resin. When done correctly, the weave of the cloth will be quite visible and NOT filled in with resin. When dry, lightly sand with 80 or 100 grit sandpaper. Then repeat the process on the top of the wing, ensuring that the top piece of glass cloth overlaps the cloth on the bottom of the wing. When finished, you won't be able to tell where the overlap is. I used Nelson Hobbies (http://www.nelsonhobby.com/paint.html) primer to fill in the cloth weave, but I'm sure there are lots of other choices for that.
In both the top and bottom covering, when the glass/resin is dry, you can carefully trim off excess clothe with scissors, X-acto knife and sandpaper.
Last note: If you ever make such a mess that it isn't salvageable, take the resin soaked cloth off the surface, throw it away and immediately clean the surface with alcohol. I had to do that once on an elevator or aileron, can't remember which. Good luck!
Regards,
Mark

Fred:
Thank you for contacting me back channel. Your Byron P-51 brings back memories... Looks like you are moving along, learning how to merge what was...with what is...today. If I may be permitted to recommend something specific I recommend you definately utilize Pacer Z-Poxy Laminating Resin in the glassing process for your wing. PacerZ-Poxy Laminating Resin is unique in that it has minimum parafin released during its cure resulting in superior interlink of any subsequent application with minimum prep.
Furthermore, I highly recommend you dilute the Z-Poxy resin "30%""after" you have mixed appropriate A~B components per the instructions on the Z-Poxy packaging. This accomplishes two things... (1) it assures you achieve the proper linking process between component A and B of the laminating resin and (2) when properly mixed the "30%" dilution of the A~B mix with "90% DENATURED ALCOHOL" will reduce the viscosity of the properly linked A~B components to permit greatest wicking to occur when "rolled" through the glass cloth during its application.
Pacer Z-Poxy is epoxy, not polyester resin. Polyester will dissolve most EPS foam...something that will ruin your day. Secondly, you should disregard any instructions in the Byron kit giving directions of how to mix their original epoxy resin...it was by mass rather than volume as is the case with the Pacer Z-Poxy...the proportions of A~B are 50/50 with Z-Poxy... Otherwise will lead to a very bad day the next morning after you do anything else....don't ask!
The only other thing you need to know is apply the Z-Poxy with a 3" wide foam paint roller to best distribute the minimum amount of epoxy you apply from the center of the wing out in all directions and over the edges of the foam components starting on the bottom side....let cure for 24 hours before trimming off excess perimeter cloth by lightly sanding perimeter with 320 grit wet/dry on a sanding block (dry)....then wipe down the glassed surface with a soft cloth soaked in denatured alcohol to loosen and remove any parafin and cloth reminants before turning it over and repeating the entire process on the opposite side.
Ed

One thing I need to mention before getting back to work... : ) Be very careful in the use of this or any spackle product as it has no load bearing property.

There are appropriate leveling products which are EPS foam safe and cure to a durable, light weight, and load bearing surface that will not easily break out on you or be soft beneath either a balsa laminate or a direct application of fiber glass and Z-poxy to your P-51 foam or wood components. One need only experience this once to suffer tremendous $ and time vestment in projects. Spackle as the directions state is meant as only a cosmetic item...not structural.
With respect to the Byron wing components I would suggest lightly sanding the entire foam surfaces to remove any sheen imparted by the molds the wings were created in. This permits wicking into the foam when Z-poxy is appropriately diluted with denatured alcohol as described above. This is not to say sand the surface in any fashion or force which will alter its shape... ;^)
The interior foam surfaces of your wing retract mounting wells can be laminated with inexpensive carbon fiber vail and diluted Z-poxy to create an exceptionally strong substrate onto which the actual retract mounting frames can be adhered. This will distribute the load of the landing impact over as wide a portion of the wing as possible to assist in eliminating gear breakouts... :^) Just an idea...






With a laminated foam you bridge the void after it is repaired per above, with balsa sheet contact adhesive adhered to the foam then the sandwich laminated with Z-Poxy and fiber glass cloth per pervious post. Since the sheeting is adhered to both sides of the foam T & C is restored with the load distributed across a broader area than that of the foam chucnk out, or crack.
The Byron wings were injection molded...not traditional ESP wings hot wire cut from blanks. The density of the Byron foam is greater, but at the same time, once compromised does not typically offer extensive wicking capability because the wing was formed from an injected hot liquid under greater compression than typical XPS (Extruded Poly Styrene) or EPS Expanded Poly Styrene resulting in a much less fisure prone composition. Please forgive my non-technical description...

Still, when tooth picks are inserted at right angles into a crack or chunck out, when the tooth picks are removed the voids created are the pathway for your repair slurry to wick into... : ) I am sure you will read an alternative shortly


I received a call from Ed today from Flite Metal. He helped me get in touch with Kelvin at Keleo Creations. This guy manufactures scale exhaust for aircraft. You can find them on the web at http://www.keleo-creations.com/
He is going to manufacture a scale exhaust for the mustang and a scale intake manifold. I can take a Fuji 50 and turn it into a rear exhaust, rear intake engine. This gives me the opportunity to tuck the 50 inside the cowling.
The exhaust stacks will have flex tubing to a custom made exhaust canister mounted to the engine.
Ed also explained to me how to make an air induction duct to keep the engine cool with minimal weight that will also vent through the belly flaps just rear of the wing.
I have included pictures for review.
This is becoming a lot of fun guys. I can’t wait to get things rolling.


The JR retracts are 4.8 volt only so if you run a 6 volt battery pack you will need
to run a regulator to an acceptable 5.2 volts.

Here is a cut and paste illustration of the flexible air duct utilized in automotive heat risers from the 60's and 70's.
Its still available in various diameters.
You open up the dump doors on the bottom of the air scoop and fuselage to permit air to vacate the engine area.
This solves the problem of an enclosed cowl on an inline engined model. I have edited the illustration to show the
exit fixture is constructed to attach to the light ply frame constructed for the rear dump door. The first one was a
little more than crude and probably confused some people... : )
Cheap to do and so easy...even a caveman can do it.... ;^)

Here is one style of flexible duct from the TransAm These are available in various sizes and wire hoops per inch.






thanks bob


Here is the piece you construct from G-10 and 1/2 (size was used only to show placement of the side balsa) square stick to mount just ahead of the rear dump door hinge point. Hot air from the engine exits through the top... Cold air from the belly scoop flows through and out the bottom slot. The actual air slot space should be as tall as permissable to scavage the most air.


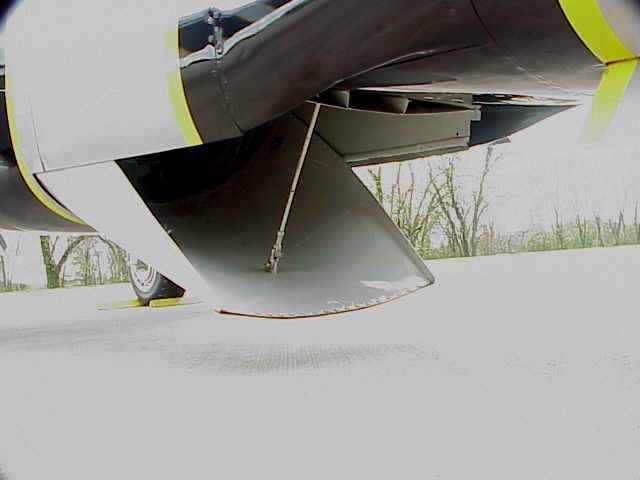
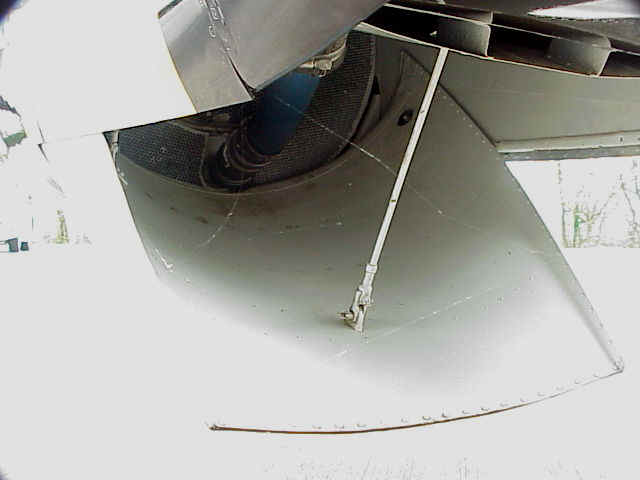
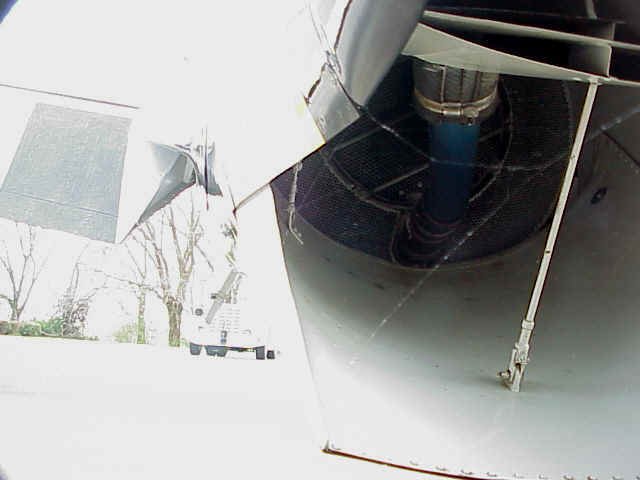
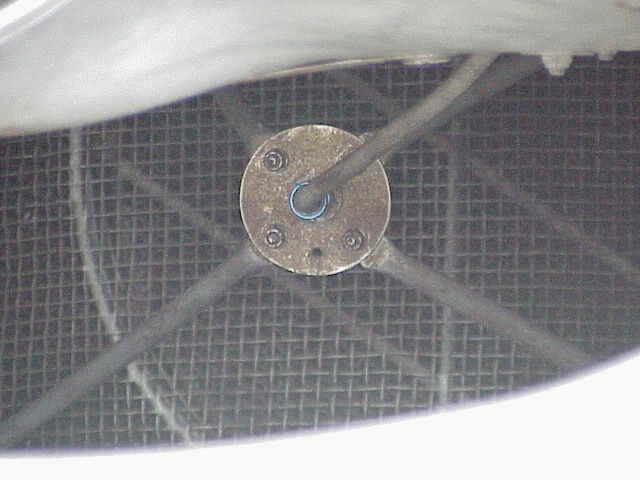
Now...we return you to Fred's build.... ;^)