TF Beechcraft Bonanza F33A Build
#153

Thread Starter
#156

My Feedback: (3)

Hola Vince,
Both wings side by side have such a high wow factor. They just look strong and confident. Next plane I build, and my choices are sport type planes, will have fully sheeted wings.
The “swept-forward sheeted area” near the root came out great. Both LEs just flow into each other so smoothly. No matter how much care I’d exercise in measuring and sanding, me centering those two sheeting edges together on top edge of R-2 would have resulted in re-tries or a modification. Like, one edge would not have sat centered on R-3. That is, if R-2 is a 3/32” rib. I would have had to fabricate/add a 1/8” false rib to insure good adhesion.
Not to inflate your ego, but I have added to my list: aluminum angle, Titebond II Premium, and Estes BT-5 Tubes. No block plane yet as I am still good at whittling and sanding.
Thanks for posting great, detailed photos. BTW, what camera are you using?
Later,
Lupe
Both wings side by side have such a high wow factor. They just look strong and confident. Next plane I build, and my choices are sport type planes, will have fully sheeted wings.
The “swept-forward sheeted area” near the root came out great. Both LEs just flow into each other so smoothly. No matter how much care I’d exercise in measuring and sanding, me centering those two sheeting edges together on top edge of R-2 would have resulted in re-tries or a modification. Like, one edge would not have sat centered on R-3. That is, if R-2 is a 3/32” rib. I would have had to fabricate/add a 1/8” false rib to insure good adhesion.
Not to inflate your ego, but I have added to my list: aluminum angle, Titebond II Premium, and Estes BT-5 Tubes. No block plane yet as I am still good at whittling and sanding.
Thanks for posting great, detailed photos. BTW, what camera are you using?
Later,
Lupe
#158

Thread Starter

Thanks Lupe, they weren't that bad to make. The flairs on the root definitely raised the difficulty level up a bit... I love sheeted wings as well. Once they are glassed and painted they will be strong and look great!
I'm not at home at the moment (quit rolling your eyes Bob!
), but I'm using a very small, fairly inexpensive Cannon. (the kind that you just point and shoot)
I'm not at home at the moment (quit rolling your eyes Bob!

Last edited by VincentJ; 08-08-2019 at 07:16 AM.
#159

Thread Starter

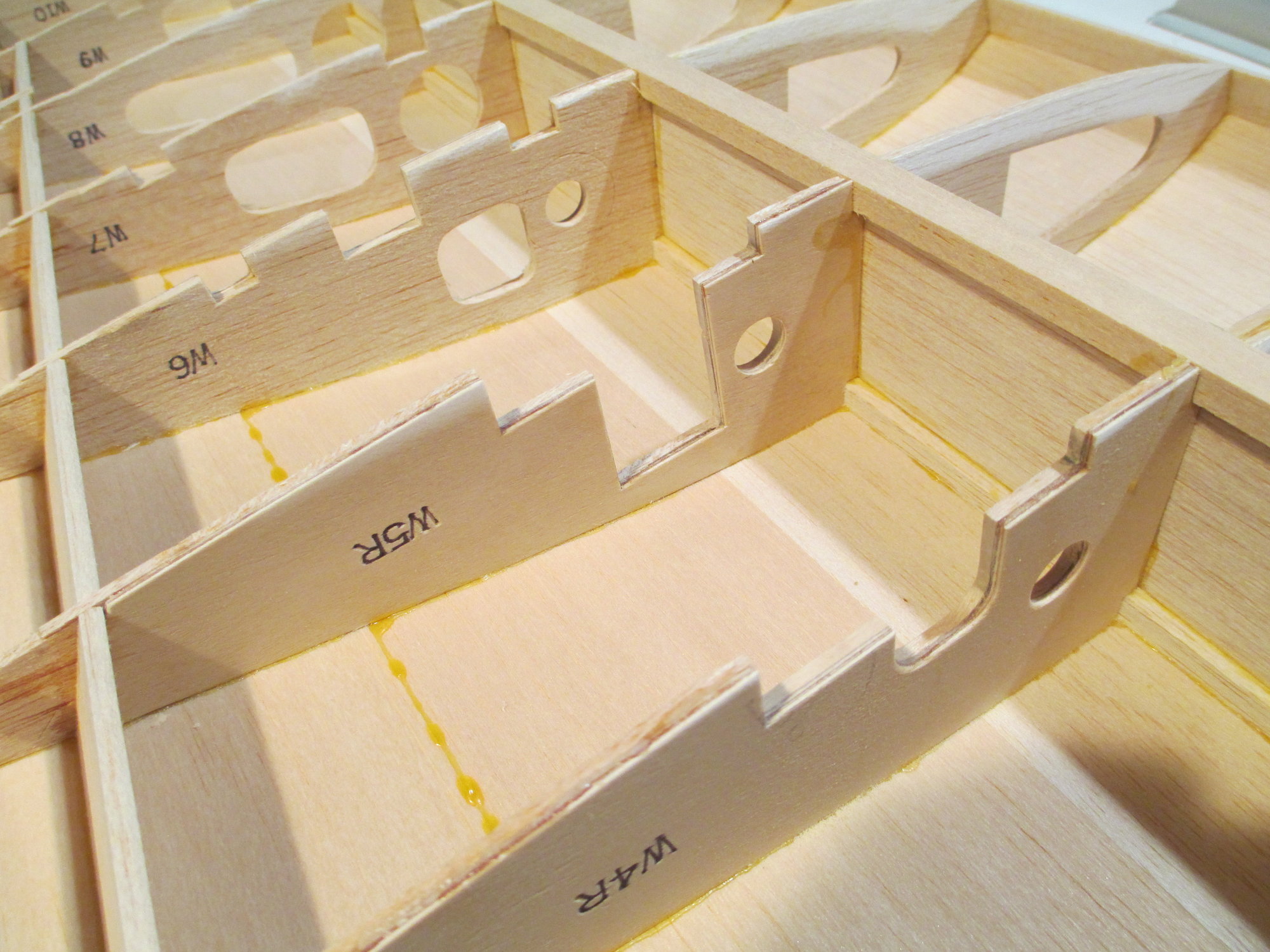
Time to epoxy one of the 1/2" x 3/4" x 6-3/4" basswood landing gear rail into place. The rail is supported by ribs W4, W5 and W6. These ribs are reinforced by epoxying birch plywood to the sides of each ribs.
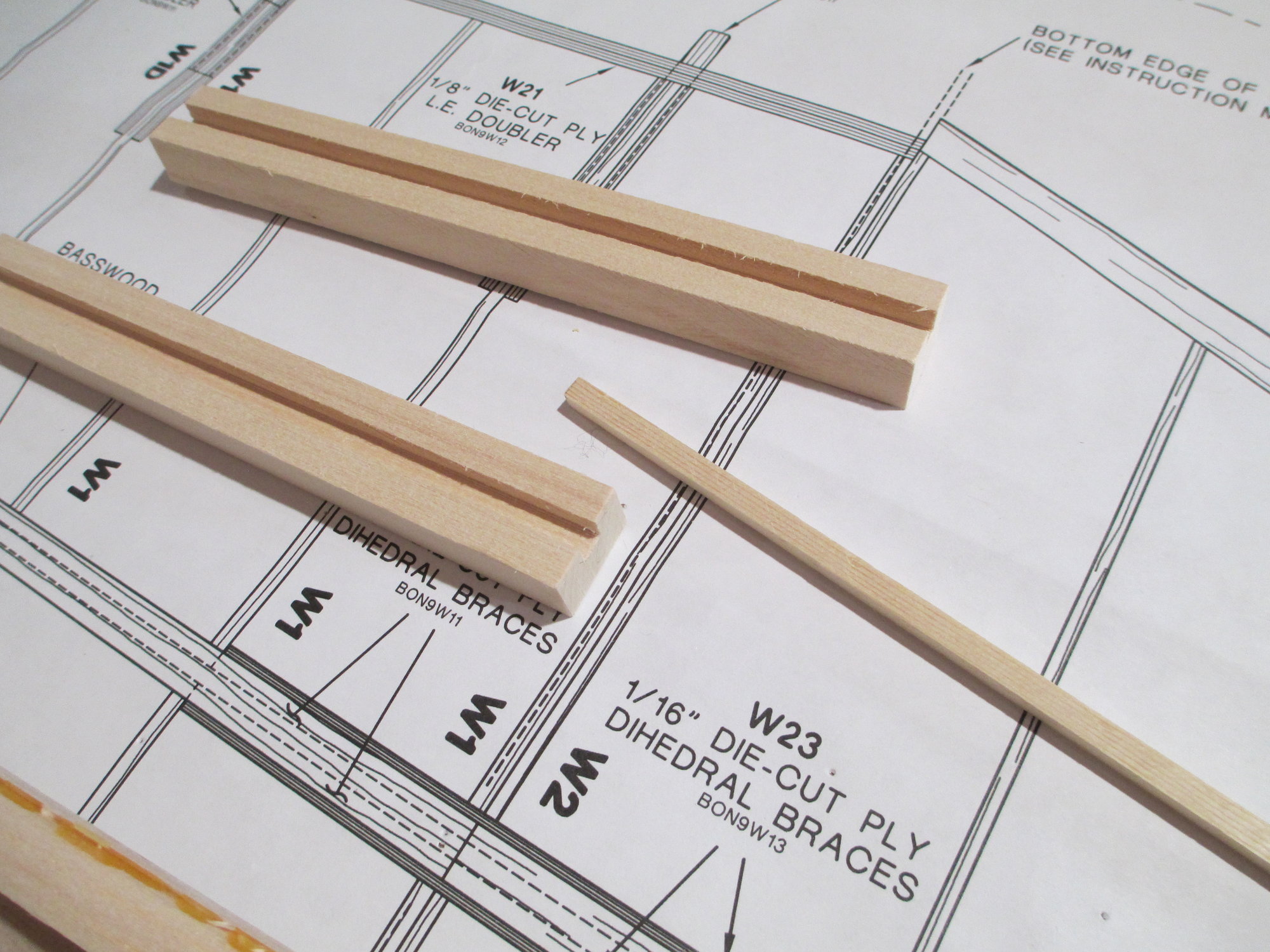
The landing gear brace has a groove cut into on one side. The other side is flush. The purpose of the groove is for the wire used in the fixed landing gear to fit into. Since retracts are being used in this application all you have to do is flip the rail over so the groove is facing down towards the top sheeting.
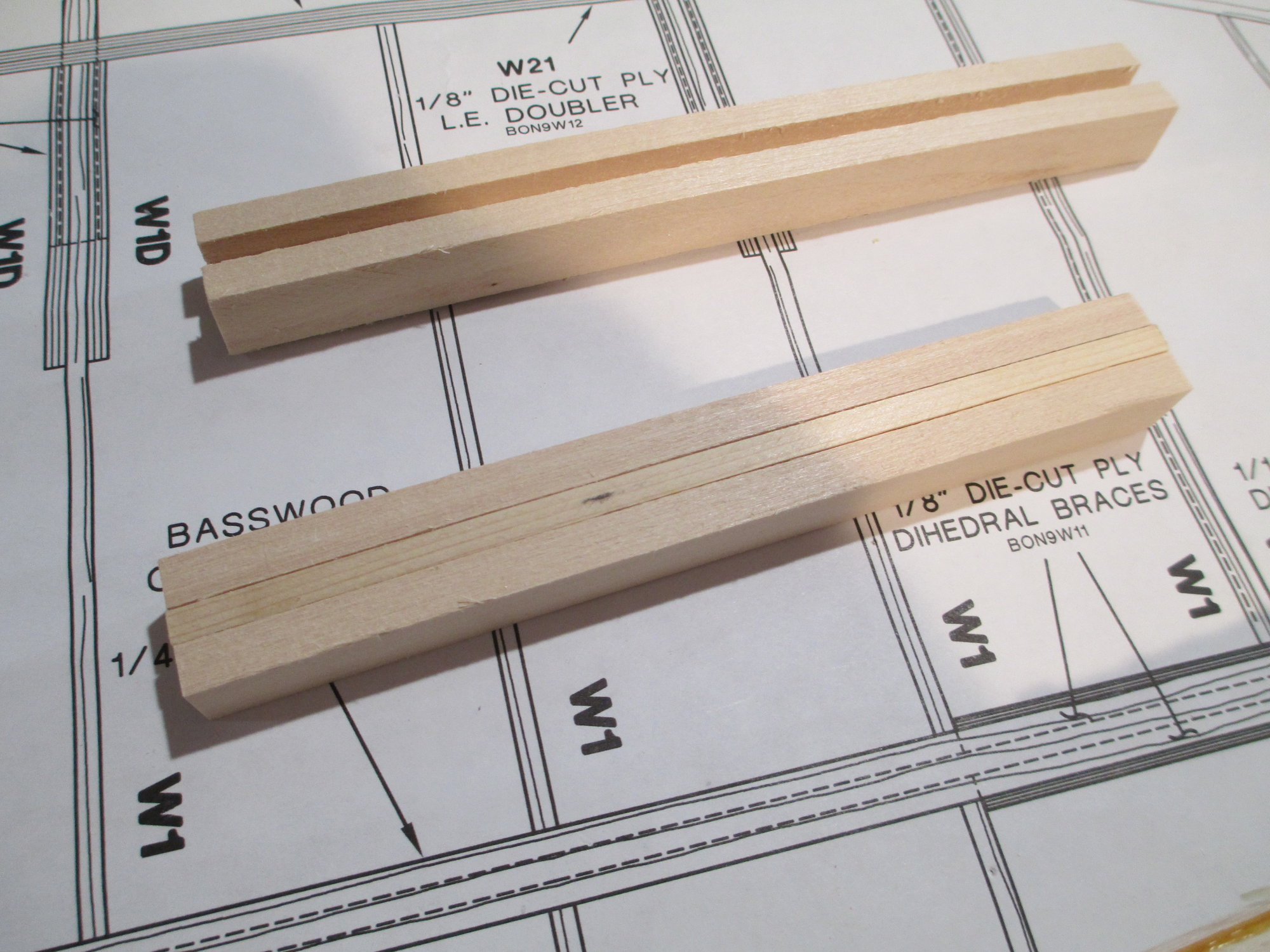
My thoughts to strengthen the rail is to fill in the groove with a piece of basswood. This will also get epoxied in place.
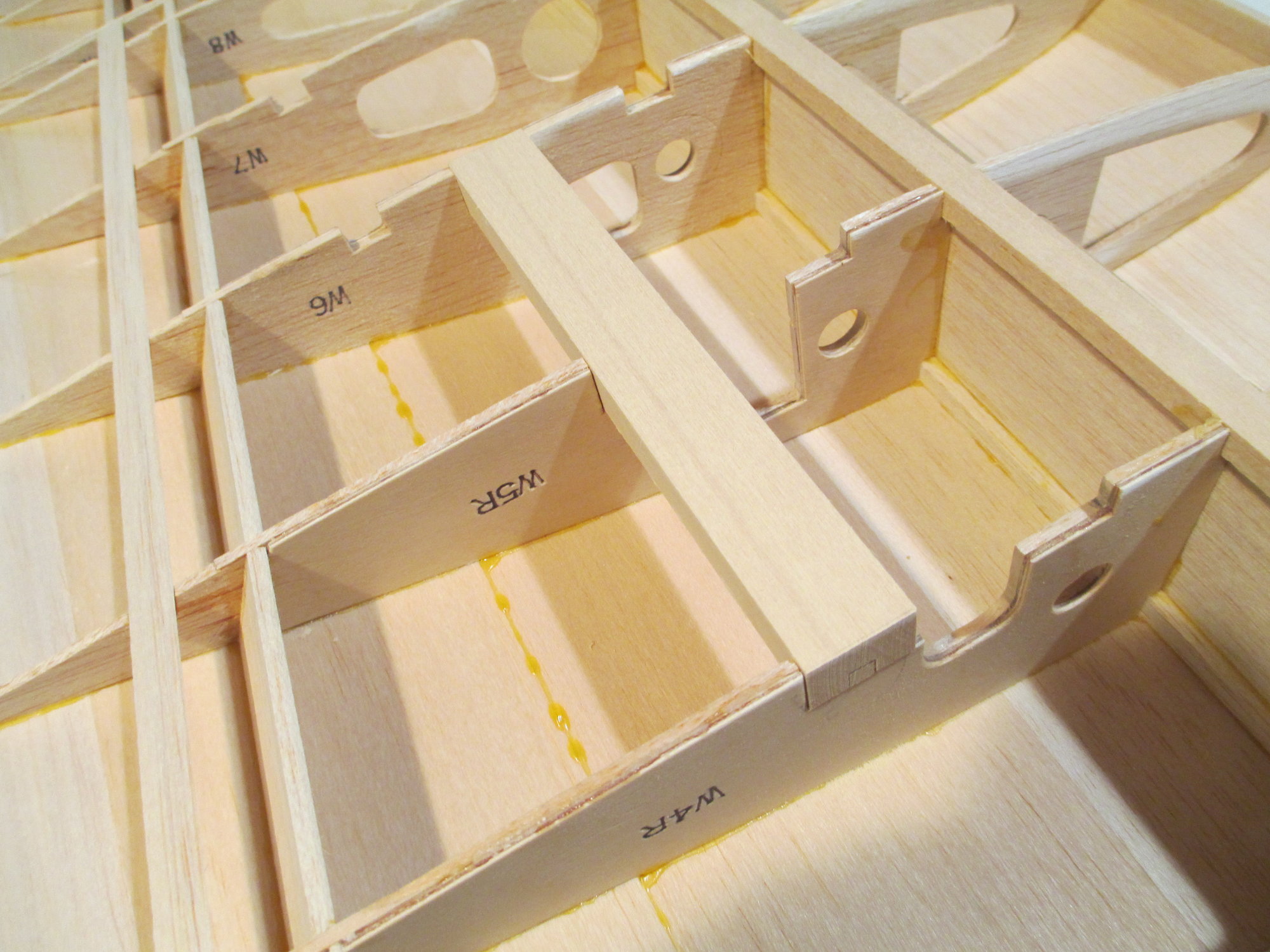
Trial fitment of the rail. Looks good, time to mix-up some 30 minute epoxy.
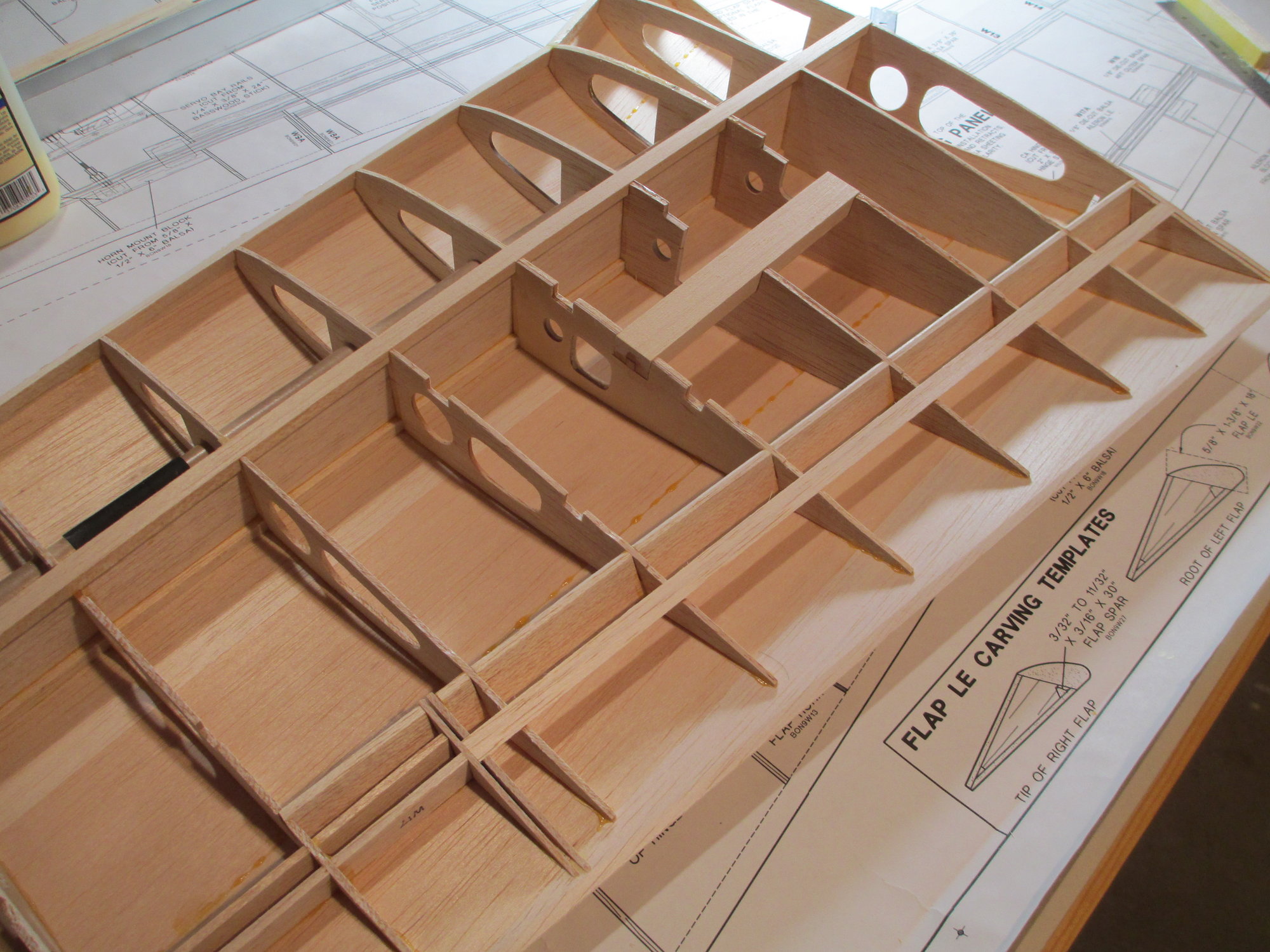
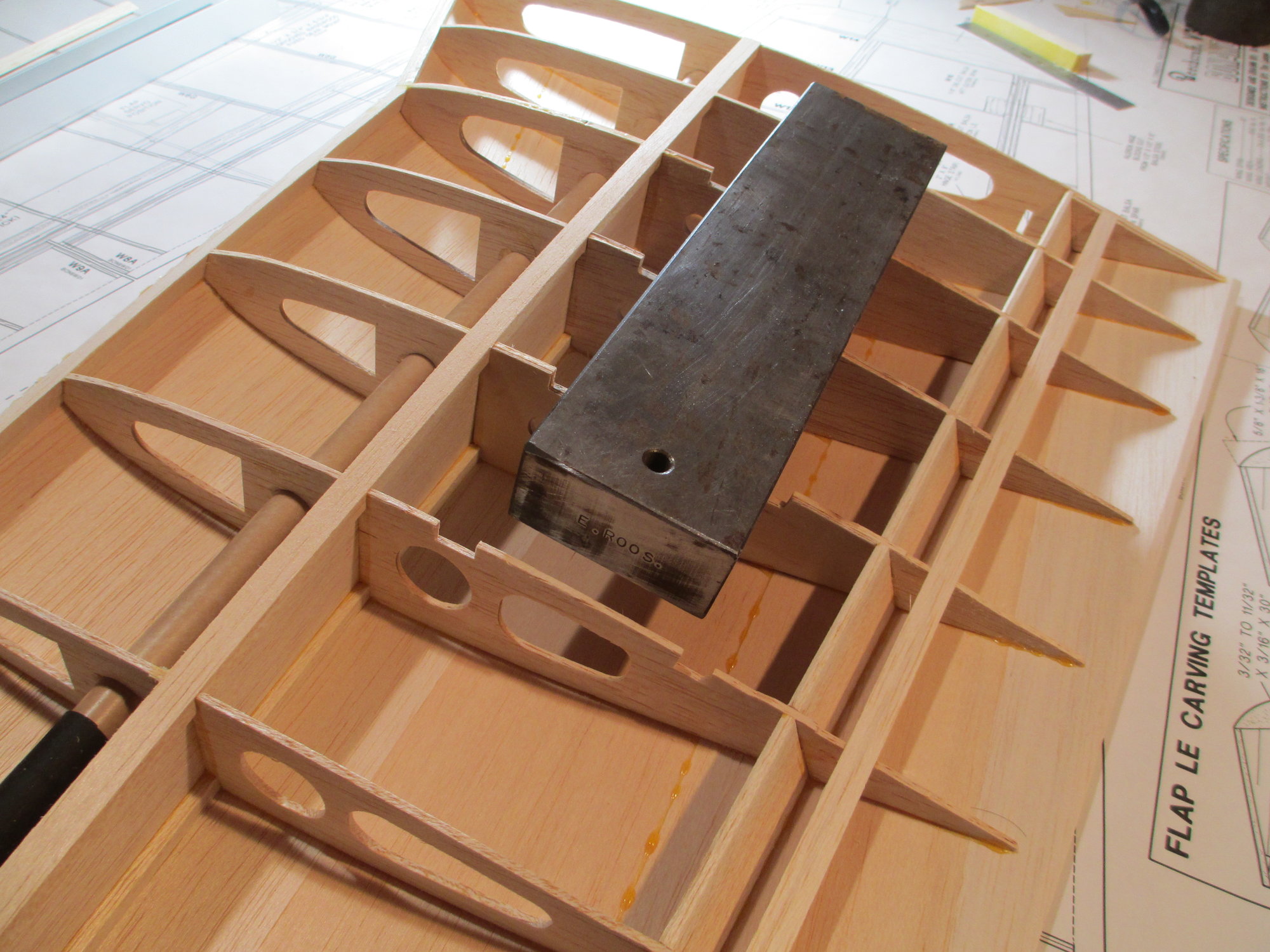
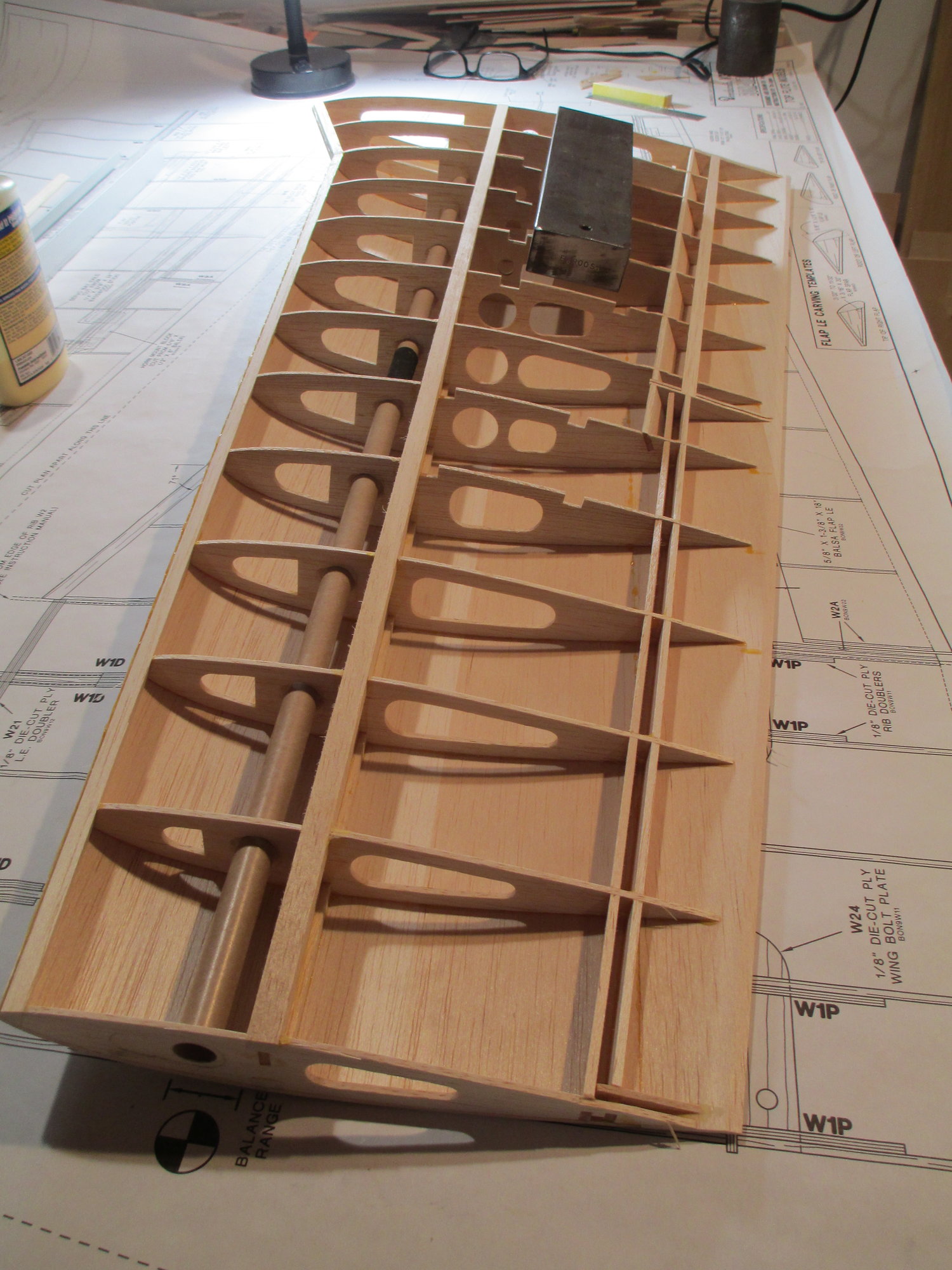
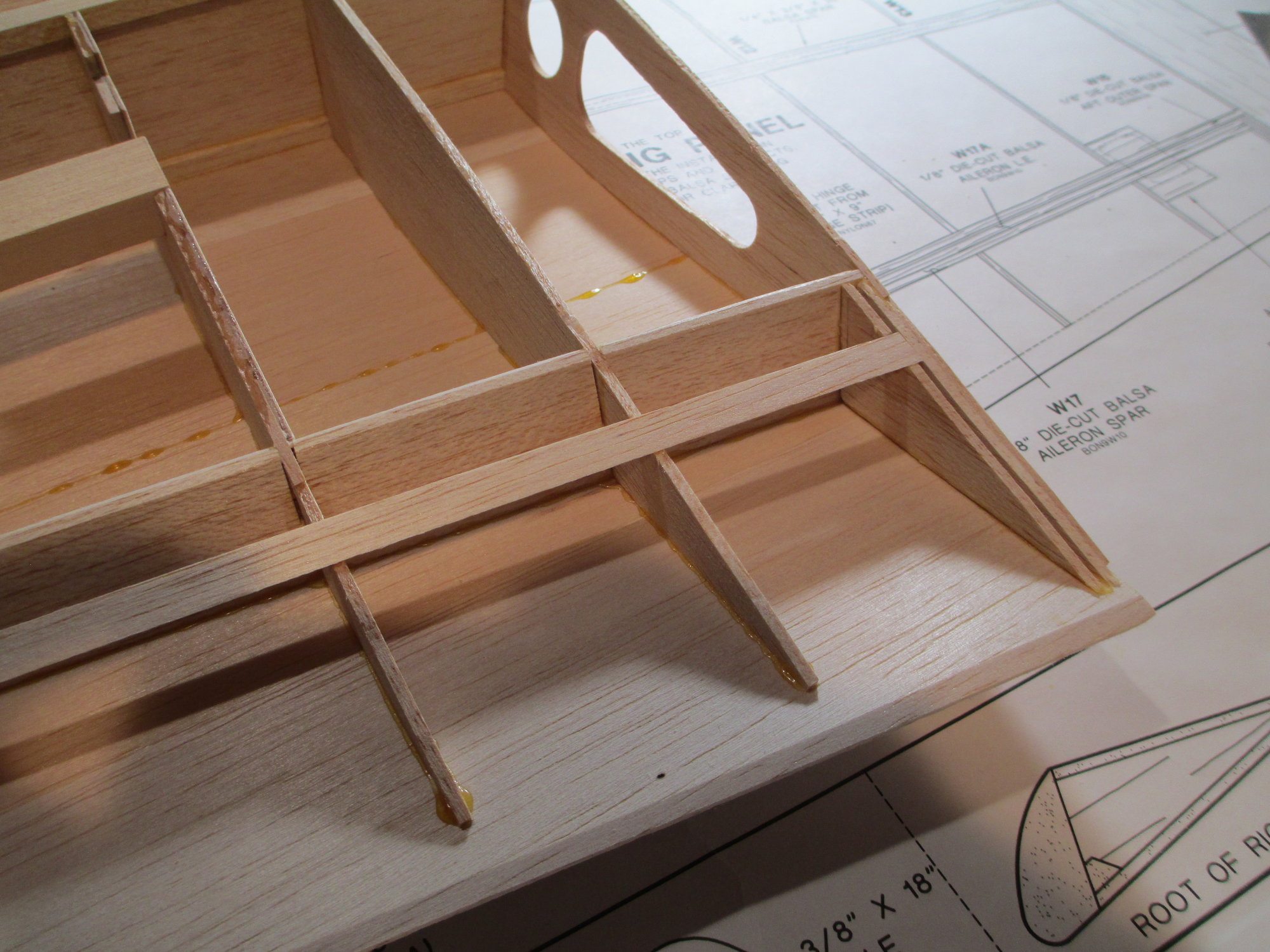
The rest of the flap and aileron structure was also added to complete the bottom of the wing. You can also see the bevel I sanded on the trailing edge of the flap/aileron.
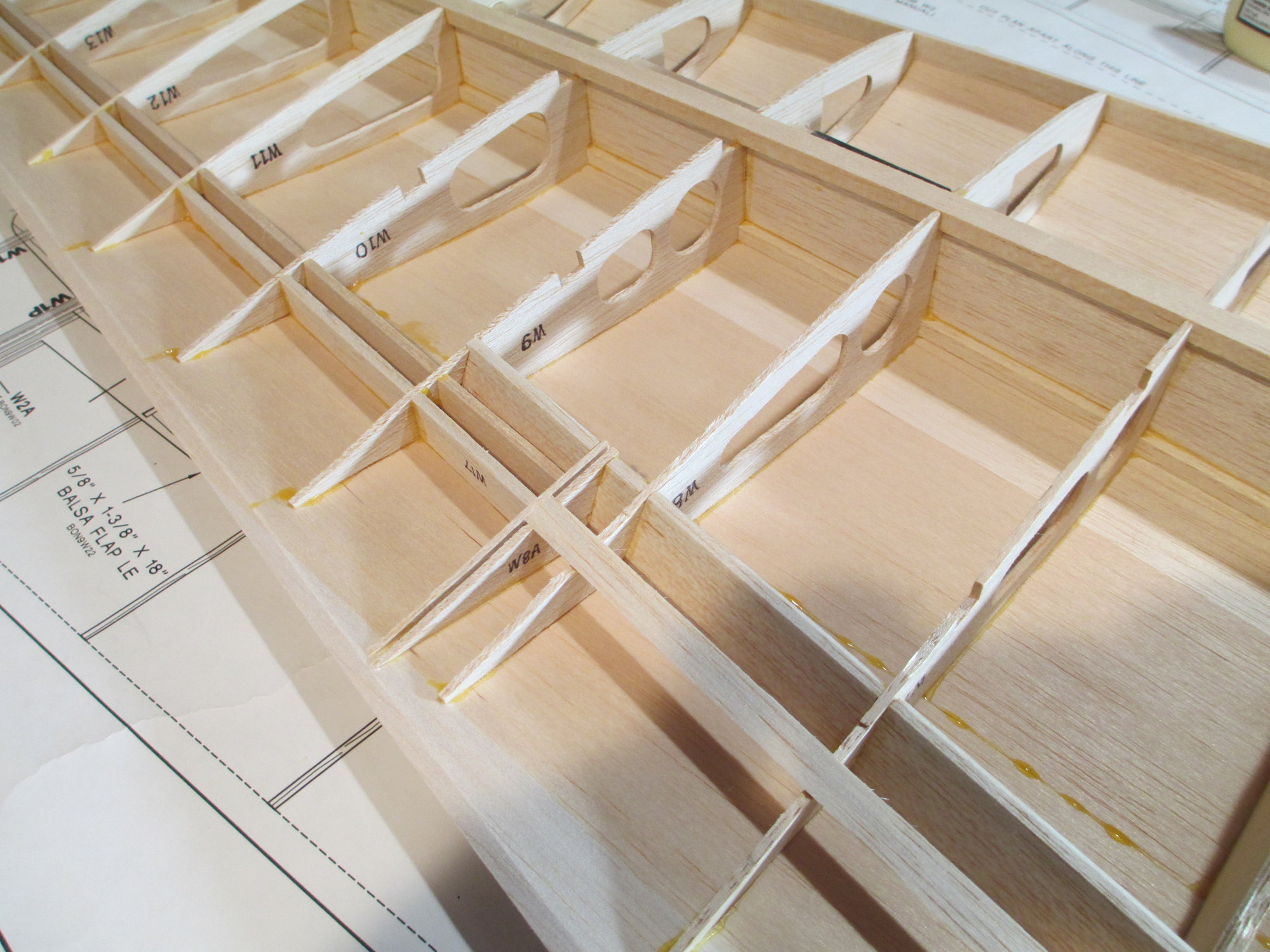
Last edited by VincentJ; 08-12-2019 at 11:13 PM.
#164

Thread Starter

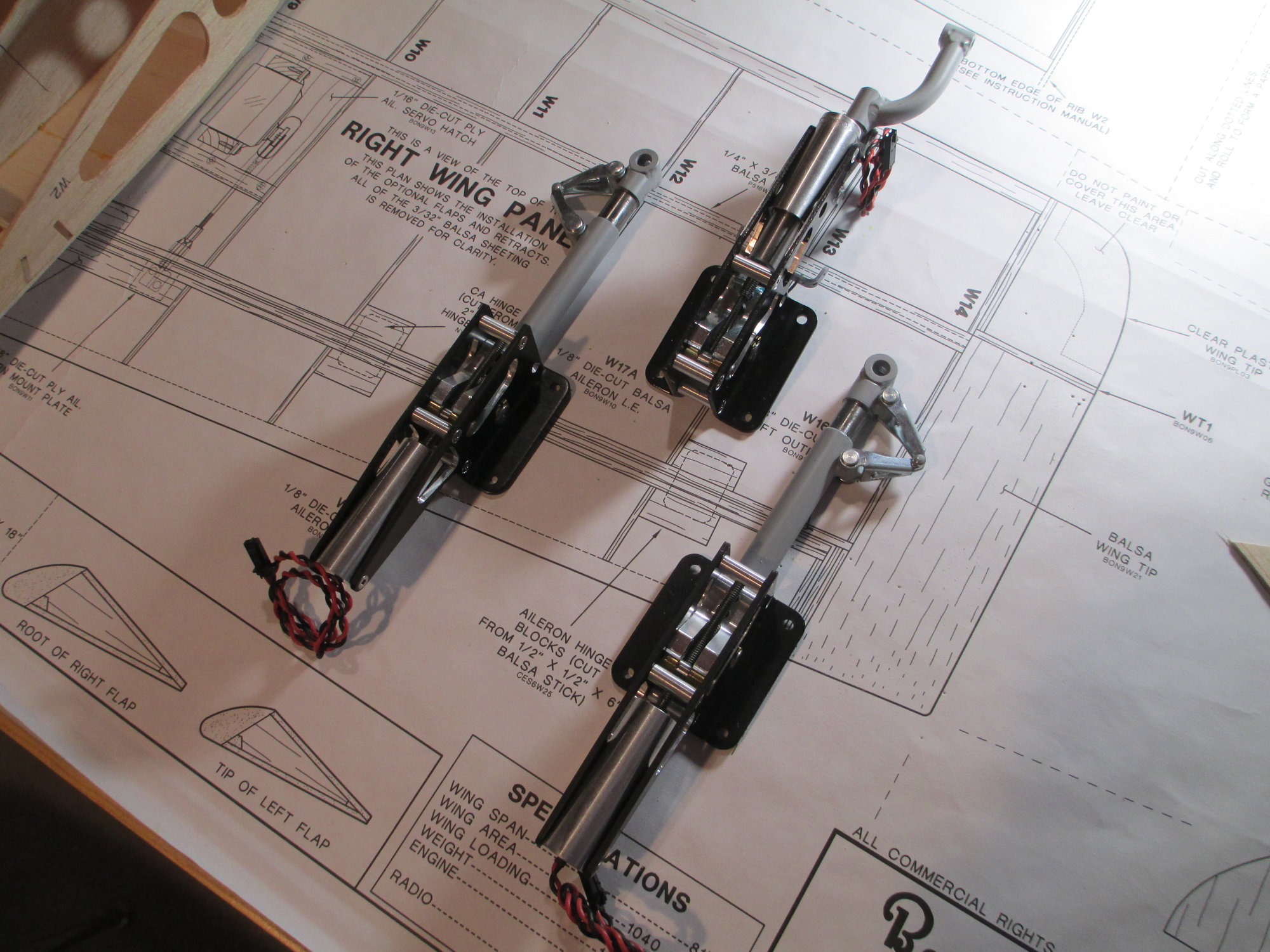
Electric retracts from Robart.
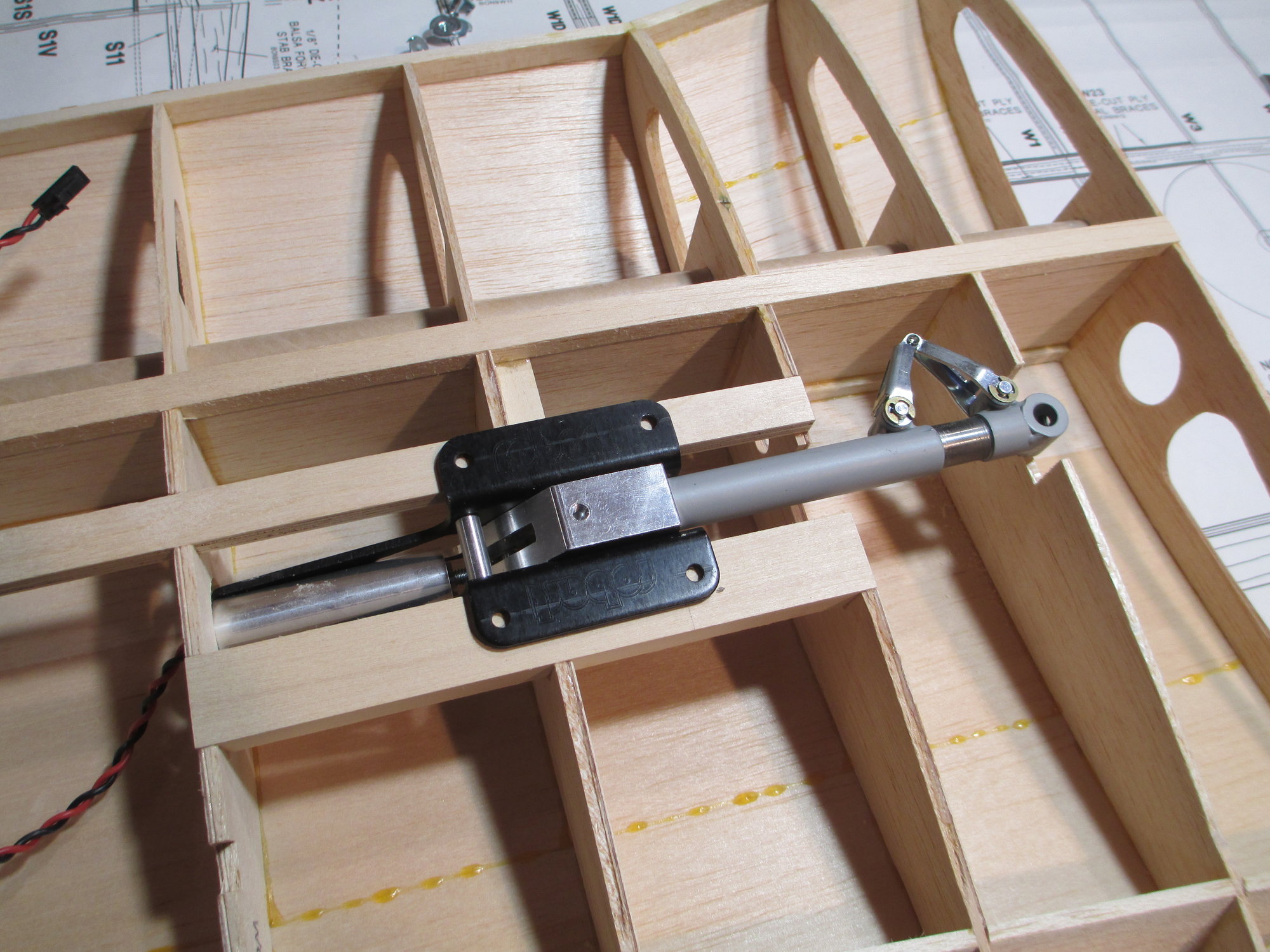
Positioned the right retract in its proper location. Note that I haven't cut out the rib to allow for the wheel as of yet.
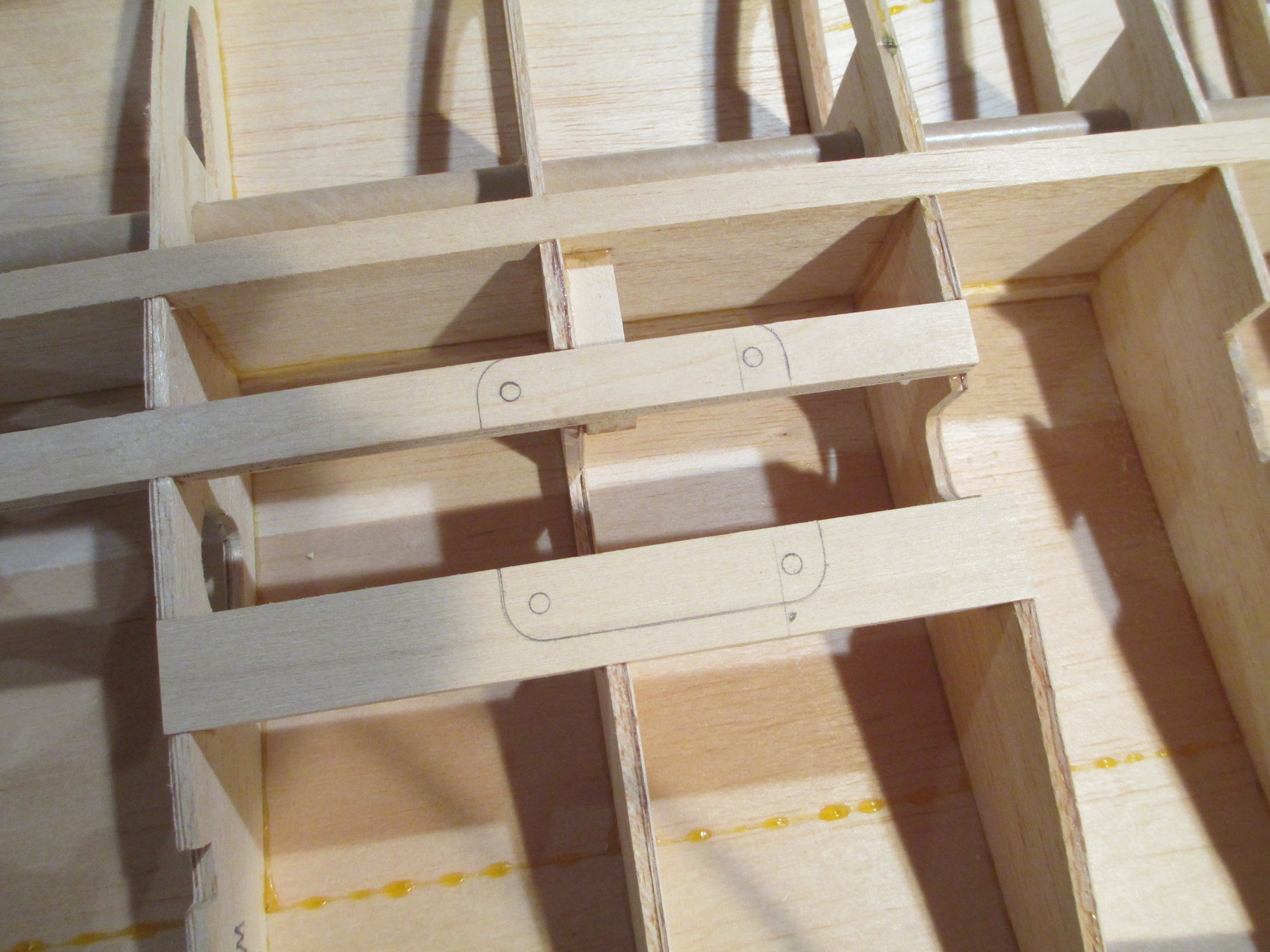
With the hole locations marked, I can drill for the mounting bolts.
#168

Thread Starter

I thought long and hard about recessing them into the rails to give it a cleaner look, but I decided against it. I am going to sheet right up to them. Retracts can be finicky, and they do require maintenance, so I wanted the ability to easily remove them should they need to be serviced... I will try to blend them in as best I can.
#169

Thread Starter
#170

Thread Starter

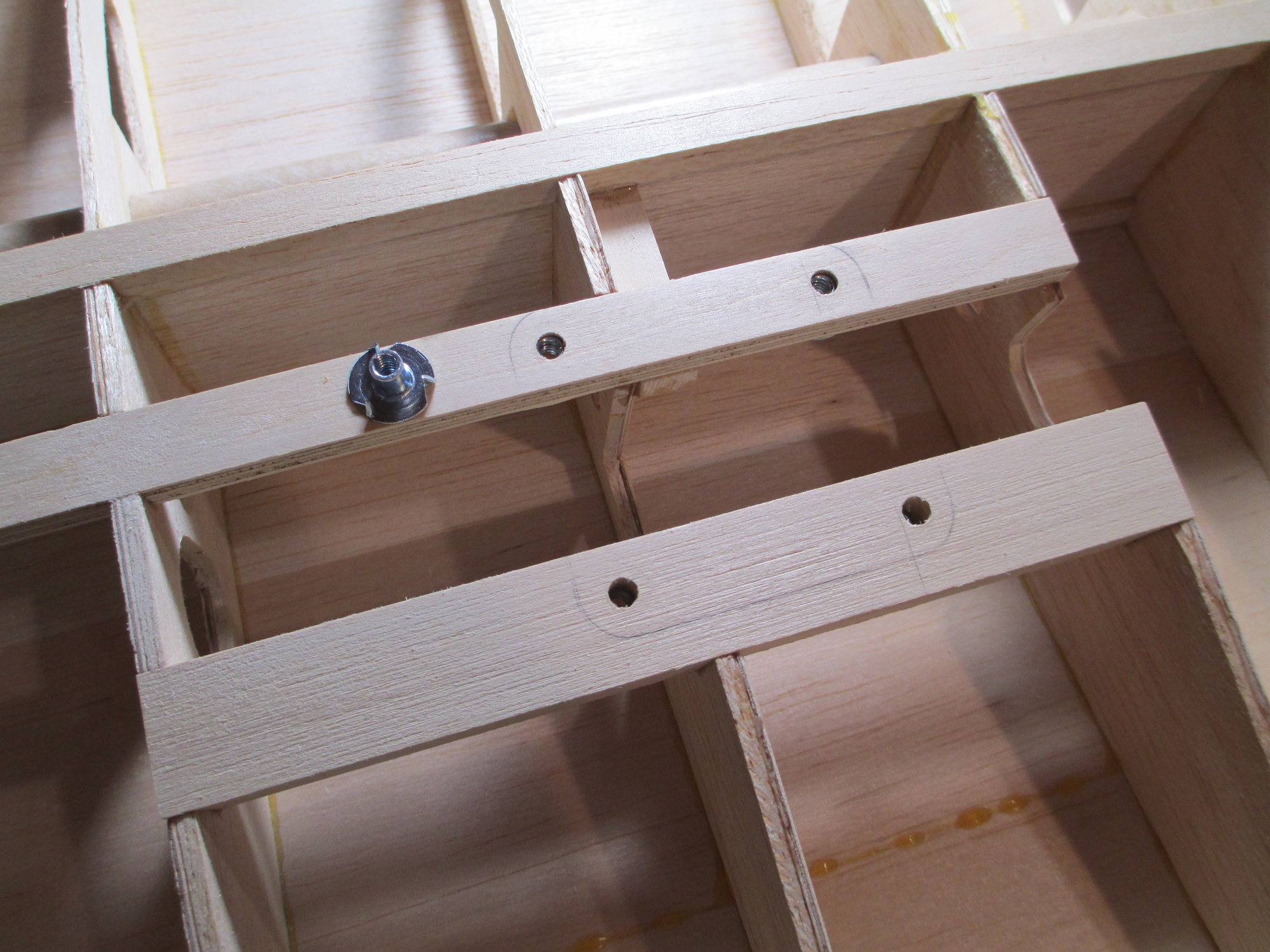
Holes were drilled to accommodate four 6-32 cap head screws. "t" nuts were used on the back side for maximum holding strength. I didn't like the idea of using screws in this application.
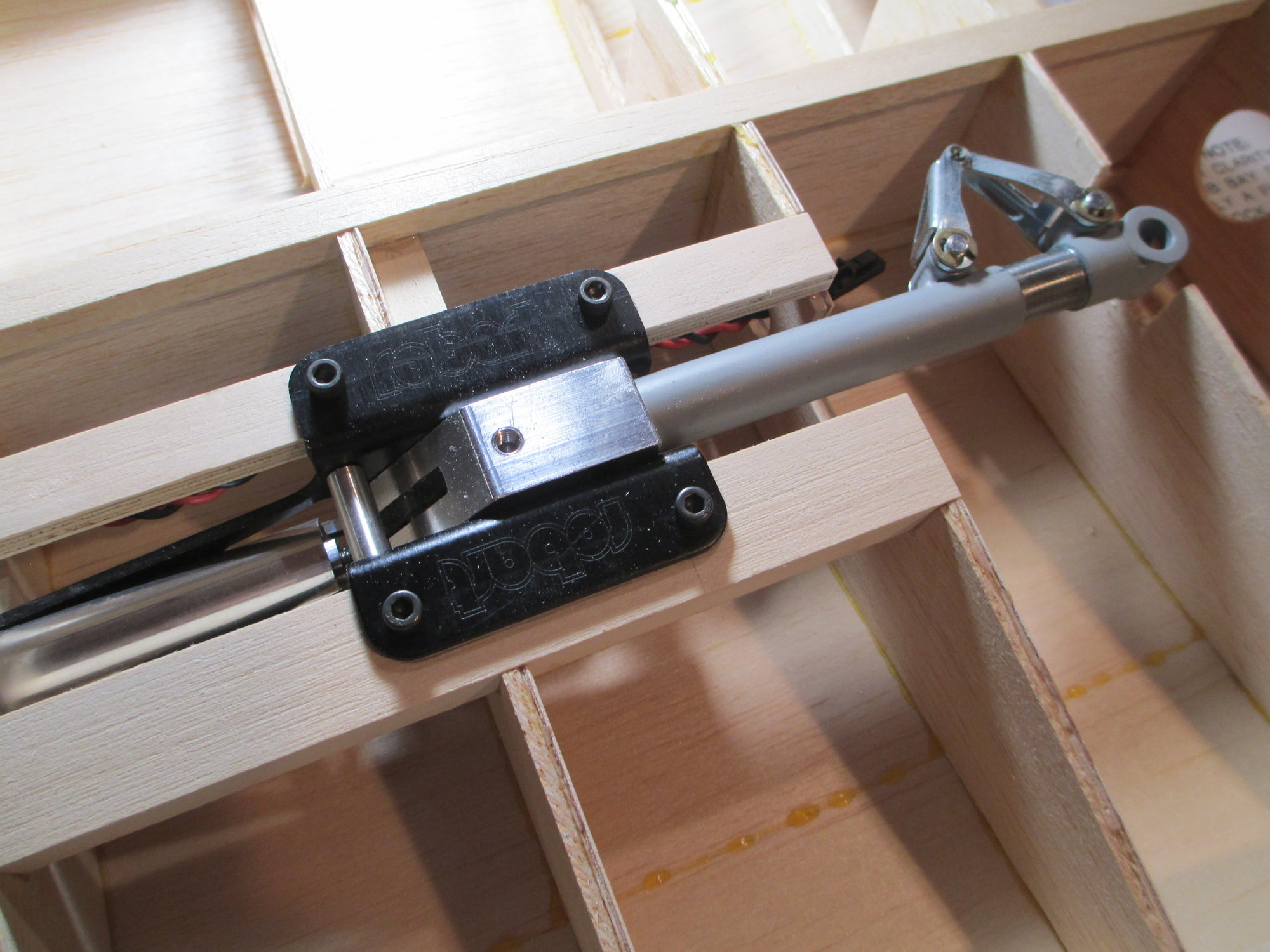
Everything aligned perfectly!
#174

That makes three of us then. I do take it a step further, however. I normally lightly scuff sand both sides of the flange of an anchor nut before I epoxy it in so the epoxy has more to grab. The platings used don't give the epoxy anything to really grab, weakening the joint.
#175

Thread Starter

That makes three of us then. I do take it a step further, however. I normally lightly scuff sand both sides of the flange of an anchor nut before I epoxy it in so the epoxy has more to grab. The platings used don't give the epoxy anything to really grab, weakening the joint.